Just-In-Time (JIT) manufacturing has proven to be a key hallmark in current management of production environments in that it helps organizations eliminate wasteful practices, increase productivity and deliver goods when they are most needed. Toyota Company was the first to introduce just-in-time, which is today an international strategy known to be implemented in many industries to reduce expenses. This post will explain what JIT manufacturing means, principles, advantages, disadvantages and useful tips for organizations that want to implement JIT successfully.
Introduction to Just-In-Time Manufacturing
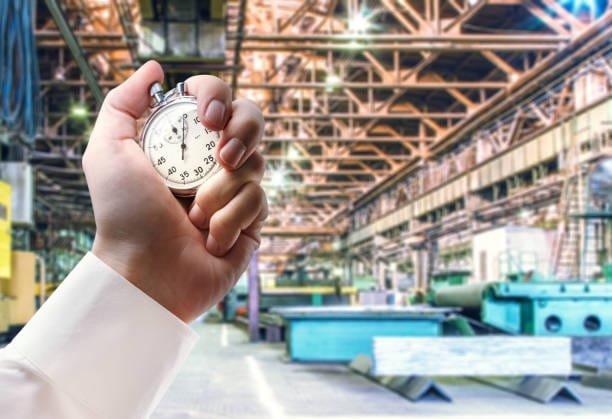
Just-In-Time manufacturing is a production system that aims at developing goods only when required in manufacturing to meet customer’s demand. JIT is an approach that replaces a more conventional manufacturing model that relies on the accumulation of inventory in a bid to ration the resources in the organization. Thus, if the production and manufacturing schedule is to be based on the true demands, the costs of inventory and other related supply chain processes can be eliminated.
Understanding the Core Principles of JIT
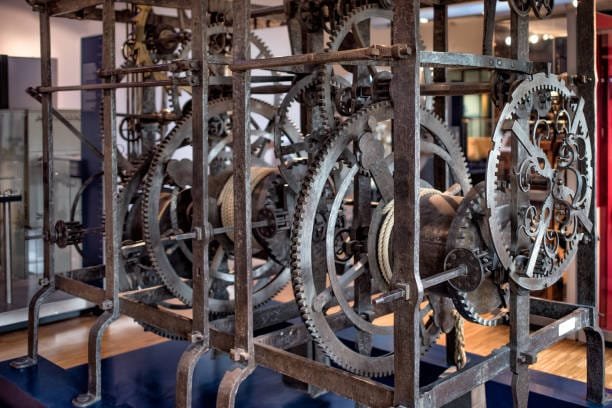
JIT manufacturing is all about principles that create efficiency, minimize waste, and keep improving the whole system. These principles form the foundation of a JIT system:
- Demand-Driven Production: The JIT systems do not use forecasts because they produce according to actual customer orders which means that the production is closely associated with customer requirements.
- Zero Waste: JIT aims at removing all kinds of waste including inventories, stocking, JIT looks into ways of minimizing unnecessary movements and other kinds of wastage in the labor force.
- Quality Control: This means in JIT wanting high quality at each operation stage since inventories cannot allow many defects.
- Continuous Improvement (Kaizen): JIT calls for continuation checks to point out areas that require enhancement, a notion known in lean manufacturing as “Kaizen.”
The Benefits of JIT Manufacturing
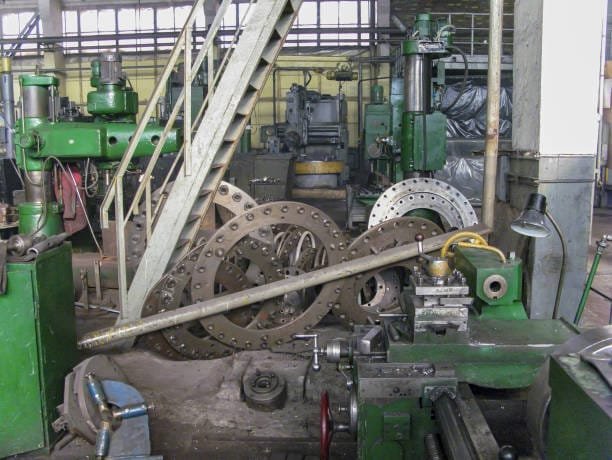
JIT manufacturing system comes along with many benefits once it has been implemented. These are not only effectiveness gains but assist in placing the production process into a ‘slimmer’ more streamlined structure.
1. Reduced Inventory Costs
One of the important benefits associated with just in time is the fact that material can be bought and used in the business without having to be stored beyond what is necessary. Consequently, the holding of inventory means that a great amount of capital is locked in stock as compared to when inventory levels are kept low.
2. Improved Efficiency
JIT aims at the reduction of squares and’s sophist warranties of waste and extraneous operations while only the value-chain relevant operations are retained. Efficiency in this process results to shorter stock cycle and lead time.
3. Higher Product Quality
The drive for consistent growth concentrates on developing and implementing solutions that assure product quality. Lower numbers of defects mean that there is less scrap and the consumer will be more satisfied.
4. Greater Flexibility and Responsiveness
JIT systems help the manufacturers to guarantee proper response to the fluctuation in customer demand or market forces. The way production process is directly connected with the demand means that companies can easily make changes to it without necessarily causing too much turbulence.
5. Cost Savings
JIT consists in reducing waste and improving production productivity that has a positive effect on its cost. These savings can therefore either be channelled back into research and development or taken to the next level to improve consumer prices.
Challenges in Implementing JIT Manufacturing
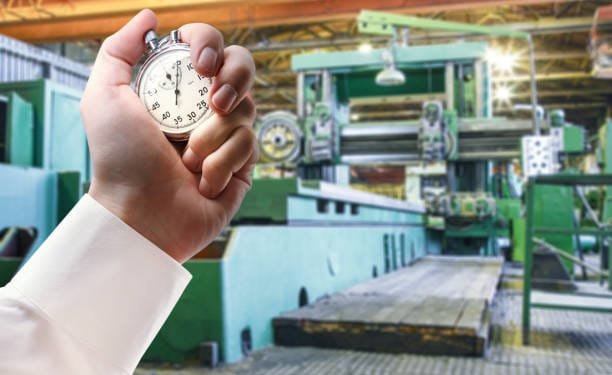
Despite the opportunities for improving the supply chain by adopting JIT, this approach has issues. Some of the difficulties that companies face in managing JIT are explained next; organizations need to be ready to deal with them to sustain an adequate JIT system.
1. Dependence on Reliable Suppliers
JIT also expected raw material to arrive on time can be a problem since any interruption will stall production. Since the material supply depends highly only on the suppliers, a strong bond is required between the company and its suppliers.
2. Vulnerability to Demand Fluctuations
JIT requires accurate demand forecasting, and changes in demand rate hence result in stock out situations or production of excess inventories. Managers require respectable methods in demand management to address such fluctuation.
3. High Commitment to Quality
Due to the fact that JIT aims to reduce inventory, there is little that can go wrong with a particular product. Managers have to ensure that quality assurance activities are integrated within the organisation in order to reduce the likelihood of having a range of avoidable problems such as increased costs by having to redo work or losing customers.
4. Initial Setup Costs
Before moving to JIT, there are costs that one has to incur in terms of technology, employee training and redesign of workflows. Despite the optimization of resources that can be obtained during the implementation of JIT, various costs are faced by businesses in the short term.
5. Operational Risk
JIT problems can occur at any time, from equipment breakdowns to lack of labor, or a shortage of materials to do the job. This in particular results in contingency planning and equipment reliability being crucial to the continuation of JIT.
Key Components of a JIT System
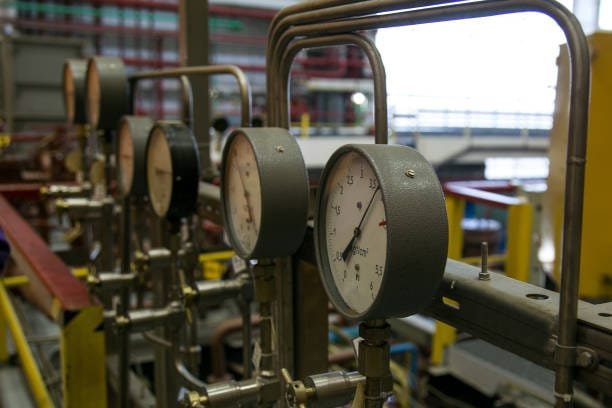
The annotated JIT system is complex and consists of several elements that must interact to support lean manufacture.
1. Pull System
A pull system is one of the JIT basic approaches whereby production is activated depending on the real customer requirements. It also has the advantage of ‘pulling’ resources, as opposed to ‘pushing’ them across the supply chain to generate the virtually certain overproduction that characterized the fully ‘push’ environment of the 1980s.
2. Kanban
Kanban, on the other hand, is a scheduling mechanism, which entails the restriction of the logistics network in JIT setting. It entails using of signals mostly in form of cards or even digital alarms to inform workers that there is need for more supplies.
3. Total Quality Management (TQM)
Thus, it can be said that the subject of this instance-‘TQM’ stands for the integral concept pointing to the strategy aimed at the constant enhancement of all kinds of quality within organizational production. In JIT environment, TQM makes sure that each of the links delivers quality output so that the chances of getting a defective product reduce.
4. Supplier Relationships
Loyalty of the supplier is critical for JIT system as it depends more on it. A good supplier assist in making certain that most of the materials needed are availed at the right time when needed, hence there will be no need to store the materials hence cutting the cost greatly.
5. Employee Involvement and Training
JIT is basically teamwork, which requires employees with practical and analytical skills, prudent enough to suggest the course of corrective of action on noticing deviations within the system. Supervisory action is essential in order to ensure that the employees of a manufacturing business become more responsive to the needs of the organization and in order to ensure that a manufacturing business can adapt quickly to the needs of the changing market.
Best Practices for Effective JIT Implementation
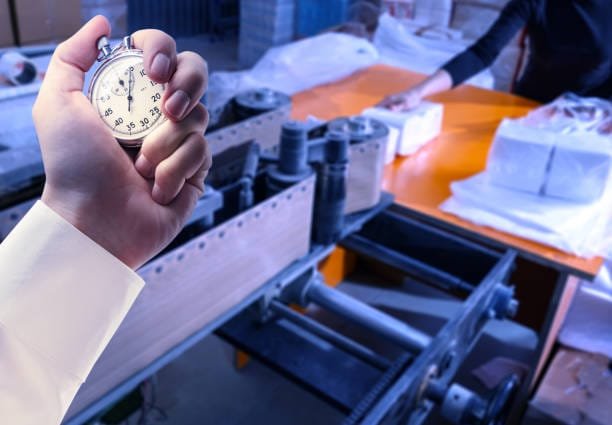
The above plan shows that it will take careful planning and a clear implementation of JIT best practices to have a successful JIT system. They do help optimize JIT and steer clear of these issues many companies may encounter in their operations.
1. Develop Strong Supplier Relationships
Pursue long term business with reliable supplier so that they could fulfill the expectation of a JIT system. Getting in touch with them often and especially keeping them informed can help avoid some of these causes.
2. Implement a Robust Quality Control System
Since the inventory is limited in JIT, quality control is of necessity. Perform routine quality assessments and involve workers in inspecting quality at the various process levels.
3. Utilize Technology for Real-Time Tracking
Ensure that technology such as the ERP and inventory management systems is used to monitor the materials and its demand in the system. This make it easier to make changes and prevent running out of stock.This also help to have a faster response in terms of stock.
4. Invest in Employee Training
Educate people at the workplace so that they can be part of change towards realizing JIT principles. Promote waste elimination as a concept where all personnel seek ways of eliminating waste.
5. Build Contingency Plans
There should be diversions in case something goes wrong with the suppliers in order to avoid affecting the company. Thus, JIT actually lacks inventory but maintaining inventory of crucial parts goes a long way in minimizing risk.
Case Study: Toyota’s Success with JIT Manufacturing
JIT manufacturing as a concept was invented by Toyota and hence it is an excellent example of how JIT manufacturing can help. The Toyota Production System that was unveiled to the world was the invention of a whole new style of lean manufacturing. Through the pull system, employing of the Kanban cards as well as the widespread mentioning of kaizen, excessive expenses were saved, unnecessary consumption was minimized as well as high-quality automobiles were maintained at Toyota. Today, TPS constitute as a leading model that industries particularly the manufacturing firms endeavour to emulate.
Conclusion
Just-In-Time manufacturing is an effective strategy for making production relevant and make improvements in reliability and efficiency. Drawing production line as close as possible to consumption, JIT reduces both costs and reactiveness to market shifts. However, JIT also needs sound supplier links, effective control of product quality, and organizational dedication to improvement. However, if organizations follow the guidelines provided below, JIT can be implemented to work for the business and help provide greater operation efficacy.